Pre-treatment of Steel
Steel substrates shall be prepared as follows:
1. Wash and degrease all surfaces to be coated in accordance with AS1627.9 with a free-rinsing, alkaline detergent, in strict accordance with the manufacturer’s written instructions and all safety warnings.
2. Wash with fresh potable water and ensure that all soluble salts are removed in accordance with AS 3894.6 methods A&D.
3. Grind all sharp edges with a power tool to a minimum radius of 2mm.
4. Power tool clean welds to AS1627.2 Class 2 to remove roughness. Remove filings, preferably by vacuum or compressed air.
5. Abrasive blast clean all steel surfaces to be painted in accordance with AS1627.4 to visual standard AS1627.9 Class 2.5 (equivalent to ISO8501-1, Sa 2.5: Very Thorough Blast-Cleaning). Use a medium that will generate a surface profile of 35 to 65 microns (as tested to AS3894.5 Method A.) In situations where it is not possible to prepare your item on all surfaces as described above, for long term protection against corrosion it is strongly recommended whenever possible, that an alternative substrate such as, aluminium be considered.
6. The steel is to be stored in an area which is clean and dry
7. The steel must be coated within 4 hours of blasting.
Application
Application Method
Electrostatic Spray
Cure Schedule
Assuming top coat applied within 12 hours:
Partially cure for 3 – 5 minutes at 120-150°C metal temperature.
This partial cure is referred to as a green cure. Green cured metal is prone to chipping/cracking if not handled with care. Ensure green cured metal is protected from mechanical damage caused by unloading/stacking.
Use top coat cure schedule to complete cure of Zincshield®.
A topcoat must always be applied.
It is recommended that Zincshield® be top coated within 12 hours due to a possible moisture uptake of the coating.
The table references AS2312.1, AS 4312 and ISO 9223 to identify the environment, conditions and atmospheric corrosivity categories.
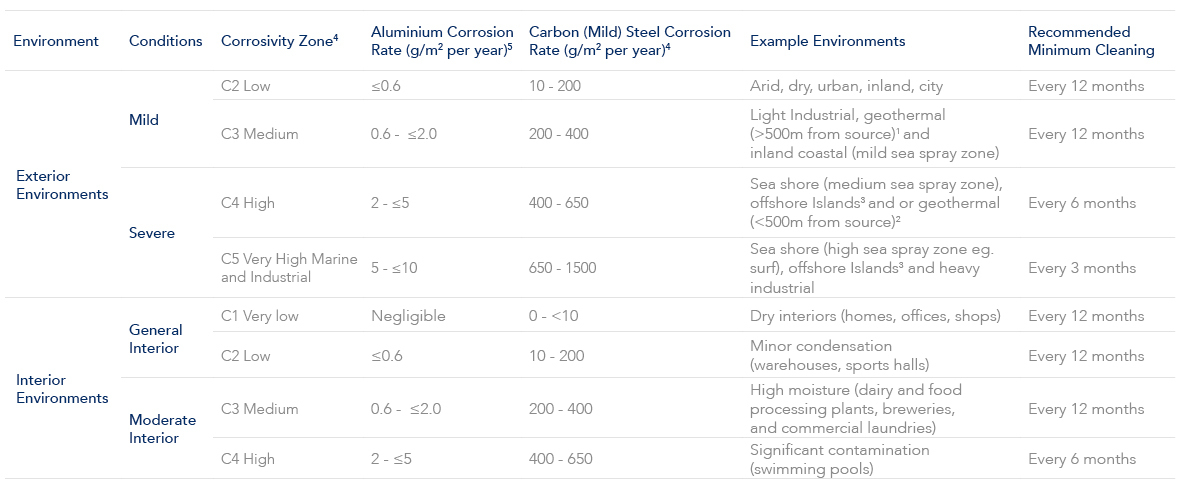
1. Geothermal environments greater than 500m of a bore, mud pool, steam vent, or other source with a pH between 5 and 9. For A pH outside this consult Dulux.
2. Geothermal hot spots within 500m of a bore, mud pool, steam vent, or other source.
3. All offshore islands including Waiheke Island, Stewart Island, Fraser Island and Pacific islands eg PNG, Fiji, Samoa, Tonga, Tahiti, Noumea
4. The corrosion rates for the first year of exposure for the different corrosivity categories of Aluminium and Carbon (Mild) Steel are determined by the following standards:
AS 4312 – Atmospheric corrosivity zones in Australia.
AS 2312.1- Guide to the protection of structural steel against atmospheric corrosion by the use of protective coatings. Part 1: Paint coatings
ISO 9223 – Corrosion of metals and alloys – Corrosivity of atmospheres – Classification, determination and estimation
5. The corrosion rates for the first year of exposure for the different corrosivity categories of Aluminium are determined by the following standard:
ISO 9223 – Corrosion of metals and alloys – Corrosivity of atmospheres – Classification, determination and estimation
Project Suitability – Steel
Zincshield is a key component of the Dulux Steel Shield™ warranty systems. Use the following table to help identify the product choice you have to gain a Steel Shield™ warranty on your project and where Zincshield is appropriate. Refer to the conditions information to determine the environment that your project will be exposed to. Click on the table below for a larger version.
All Dulux powder products are NOT suitable in strongly acidic or caustic environments so the pH must be between 5 and 9.
1. Fluoroset may be suitable in locations <10m from the high tide line e.g. harbours (contact Dulux for advice.)
2. Protexture, Duratec and Electro are only suitable for coastal environments >10m from the high tide.
3. Duralloy and Precious are only suitable for coastal environments >100m from the high tide line.
* In Mild (Medium) exterior environments and Moderate (Medium) interior environments a 10 year corrosion warranty is available with a Zincshield, E-Prime and the indicated top coat system. Without E-Prime a 5 Year corrosion warranty is available.
** Duratec Intensity – Steel Colour Warranty 15 Years.
Please refer to Interior and exterior environments close to liquids for warranty implications where powder coatings may be in close proximity to liquids other than the sea.
Steel Shield – Interior environments
All Dulux powder products are NOT suitable in strongly acidic or caustic environments so PH must be >5 and <9.
1. In Moderate Interior (medium) environments 5 year corrosion warranty is available with a Zincshield and the indicated top coat system.
2. In Moderate Interior (medium) environments 10 year corrosion warranty is available with a Zincshield, E-Prime and the indicated top coat system.
*Duratec Intensity – Steel Colour Warranty 15 Years.
Please refer to Interior and exterior environments close to liquids for warranty implications where powder coatings may be in close proximity to liquids other than the sea.
Conditions
Use the following table which references AS2312.1, AS 4312 and ISO 9223 to identify the environment, conditions and atmospheric corrosivity categories
To pinpoint your projects corrosivity zone this table should be used together with the corrosivity zone maps contained within AS 4312.
1. Geothermal environments greater than 500m of a bore, mud pool, steam vent, or other source with a pH between 5 and 9. For pH outside this consult Dulux.
2. Geothermal hot spots within 500m of a bore, mud pool, steam vent, or other source.
3. All offshore islands including Waiheke Island, Stewart Island, Fraser Island and Pacific islands eg PNG, Fiji, Samoa, Tonga, Tahiti, Noumea
4. The corrosion rates for the first year of exposure for the different corrosivity categories of Aluminium and Carbon (Mild) Steel are determined by the following standards:
AS 4312 – Atmospheric corrosivity zones in Australia.
AS 2312.1- Guide to the protection of structural steel against atmospheric corrosion by the use of protective coatings. Part 1: Paint coatings
ISO 9223 – Corrosion of metals and alloys – Corrosivity of atmospheres – Classification, determination and estimation
Environments close to liquids other than coastal, river and lake salt water environments
Zincshield suitability for environments close to liquids other than the sea is dependent on the top coat choice.
Please refer to the guidance below for:
- Any interior application of powder coating close to liquids, eg swimming pools, fountains, bathrooms, showers, sinks etc
- Buildings that have exterior facilities close to liquids other than the sea, eg outdoor swimming pools, fountains, outdoor bathrooms
1. Aggressive liquids such as Chemically Treated liquids and Salt Water must be cleaner off immediately as per the Dulux Care and Maintenance guide.
Please note chemically treated water includes antimicrobial treatments, e.g. in pools, anti-corrosive chemicals, and soapy water in bathrooms and showers.
■ Where indicated Steel Shield warranties are available on areas >than 1m from the liquid.
✓ Where indicated Steel Shield warranties are available on areas >than 2m from the liquid (ie outside the splash zone).
○ Where indicated Steel Shield warranties are available on areas >1m from the liquid on interior applications and >2m on exterior applications
● Where indicated Steel Shield warranties are available any distance from the liquid.
Steel Shield warranties are only available when applied by a Dulux Accredited Powder Coater to the warranty specification on recommended project types and conditions.
All Dulux powder products are NOT suitable in strongly acidic or caustic environments so the pH must be between 5 and 9.
Steel Shield warranties are not available if the powder coating is immersed in any liquid.
Advice Line
Our dedicated consultants can help simplify the specification process, saving you time and money by providing the right coating advice for your project.
Call 13 24 99